Welding
With a history in pressure equipment manufacture, welding for LA Services has always been about compliance, integrity and reliability. These inherent process values, ingrained into our production activities also hold for welding as service, whether these skills & knowledge are applied to the repair of a gelato machine or a high pressure natural gas pipeline we are committed to providing our welding expertise to your next workshop or site welding project.
We use the following welding processes
SUBMERGED ARC WELDING
Our SAW capabilities are underpinned by two Lincoln Electric Tandem Twin boom machines, a portable boom unit, a nozzle to shell and internal SAW machine, as well as a custom built ‘double header’ developed as a distortion control capability for welding air cooler header boxes.
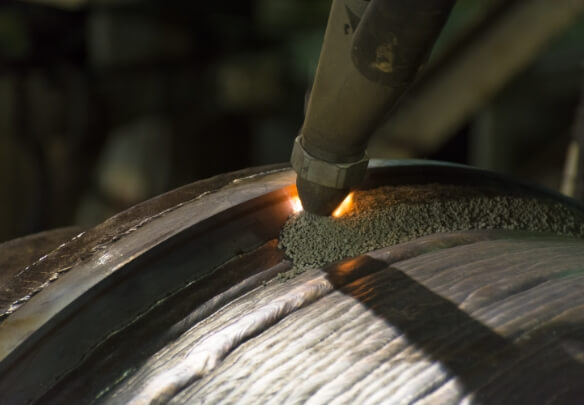
GMAW
LA Services introduced Lincoln Electric Surface Tension Transfer (STT) process to pipeline welding in 2006 and have been incorporating it into projects ever since. It is now part of our in-house apprentice training program alongside traditional TIG root methods. We maintain a fleet of conventional GMAW and STT machines to support rapid production ramp-ups for pipeline, shutdowns or major project works.
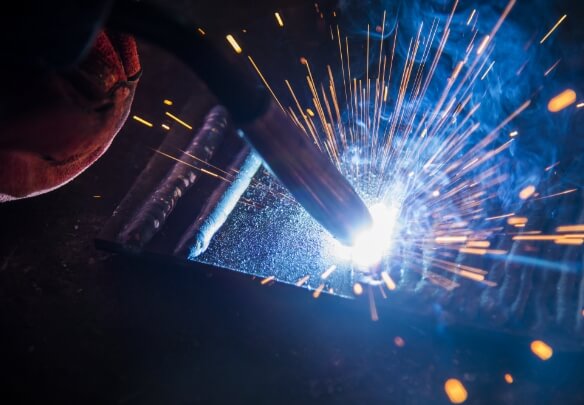
Gas Tungsten Arc Welding
Remains an important process to both our production and site welding activities, for this reason we invest in cross skilling our welders in this and the other day to day processes used by LA Services to ensure production flexibility can be offered by our trades team.
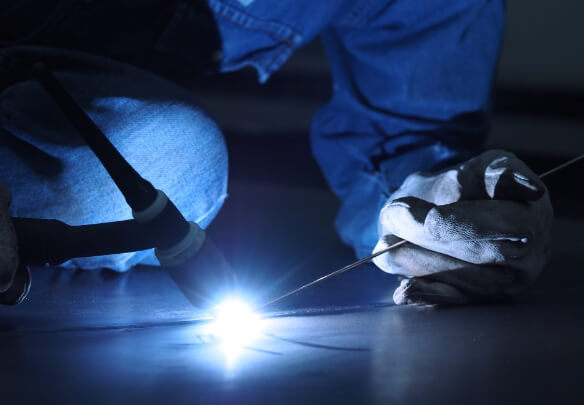
Manual Metal Arc Welding
Manual Metal Arc Welding is utilised primarily for servicing gas pipeline site welding activities. Like other welding processes, MMAW is part of our inhouse apprentice training scheme ensuring this technology and technique has the skills and resources to continue servicing gas infrastructure works.
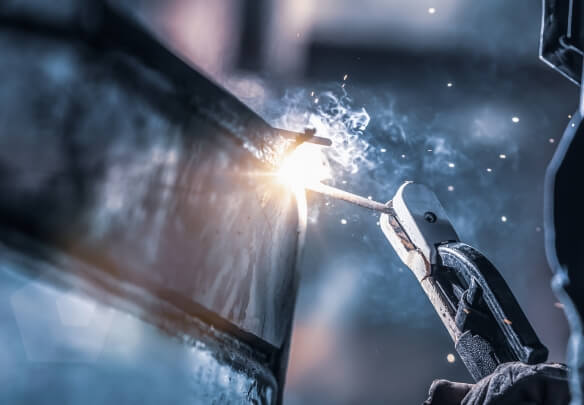
OUR UNIQUE WELDING DISCRIMINATORS
40 years of compliance welding
Critical environment welding
Material diversity & thickness range expertise
FULL RANGE OF WELDING SERVICES
Get In Touch
Drop us a line to discuss your product or service solution requirement